多摩地区 株式会社アスペクト
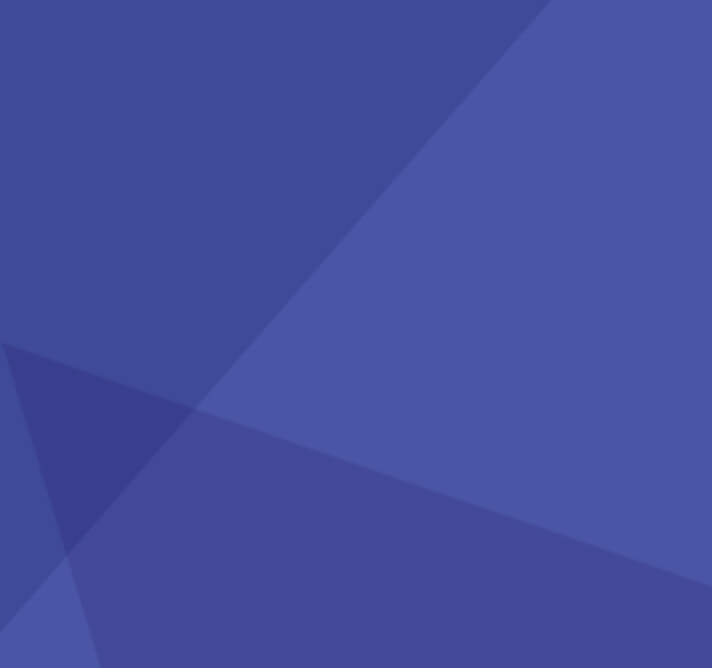
株式会社アスペクト
3Dプリンターの開発にいち早く着手。先端技術が製造業の未来を切り開く
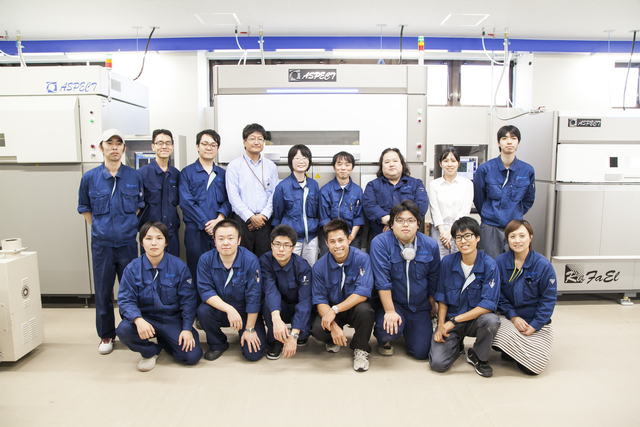
株式会社アスペクト
3Dプリンターの開発にいち早く着手。先端技術が製造業の未来を切り開く
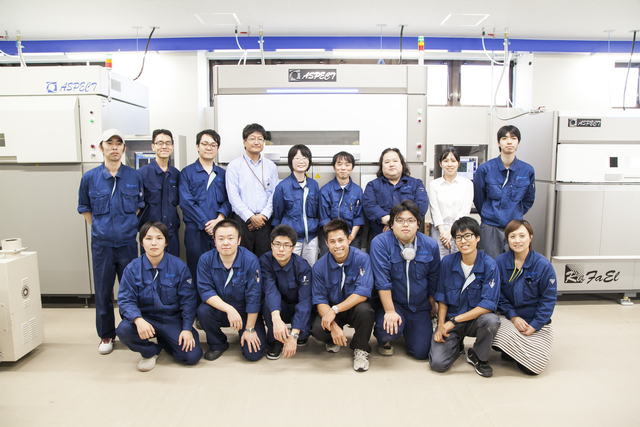
技術開発ストーリー
3Dプリンターの開発にいち早く着手。先端技術が製造業の未来を切り開く
コンピュータで設計した3Dデータから部品や模型を製造する3Dプリンター。魔法の箱、あるいはものづくりを革新するなどと近年、脚光を浴びている。しかし、この技術、決して真新しいものではないという。アスペクトの代表、早野誠治氏は、四半世紀以上前にこの造形技術と出会い、いち早く装置開発に着手。現在はプラスチックのみならず金属や新素材による造形といった新たな挑戦に乗り出している。
3Dプリンター技術と出会い、独立を決心する
3Dプリンターは、アディティブ・マニュファクチャリング(AM)という技術によって造形物を作っている。アディティブとは「足す」、「付け加える」という意味でマニュファクチャリングは製造を意味する。つまり、プラスチックなどの素材を立体的に重ねていくことで物を作る技術である。この技術を使えば金型いらずで試作品が作れるためコストや製作期間を大幅に削減できる上に、CADデータを変えるだけで容易に何パターンもの試作品を作れる。加えて、生産スピードや製品強度の向上が目覚ましく、試作品のみならず製品を最終製品として多品種少量生産も可能になると期待されている。
この技術を一躍有名にしたのはオバマ米大統領。2013年の一般教書演説で、あらゆるものづくりに革命を起こすと3Dプリンターを評し、研究開発の大規模強化を表明。人々は一気に画期的技術に傾倒したのである。その演説から遡ること27年前、このAM技術を目の当たりにし、その革新的技術に衝撃を受けていたのがアスペクトの代表、早野誠治氏である。当時、大手商社に勤めていた早野社長はAM技術の時代を予感、翌年には装置開発と事業化に乗り出した。
「何かの部品や製品を作るには、素材を切り出したり削ったりして作るか、金型で成形するといった製法になるのですが、AM技術を駆使すれば、素材にレーザーを照射するだけでどんなに複雑なものでも簡単にできてしまうと考え開発に乗り出したんです。ただ、弱点もあったんですよね」
と当時を振り返るのは、光造形装置の研究開発チームを率いていた萩原正さん。その弱点とは強度が極端に弱いことだ。ものによっては落としただけで壊れてしまうこともあった。そのデメリットがある以上は、製品を作る前段階の試作品にはなりえても、最終製品としては使えない。そこで目をつけたのがプラスチックなどの素材の粉末を使った新しい造形法、PBF(Powder Bed Fusion:粉末床溶融結合法)だった。テキサス大学が開発した技術で、粉末を敷いて固めたい部分にレーザーを照射することで融かし、凝固させることで層を作り、その層を重ねることで造形するというもの。この技術なら強度が出せるため、試作品から量産品まで対応できる。そう確信した早野社長だったが、すぐにその装置開発には乗り出さなかった。まずは、PBFの3Dプリンターの魅力を広め、マーケットを切り開くことが先決だと考えたのだ。そこで、テキサス大学が設立した企業から日本での装置販売権を取得し、装置の輸入代理店兼、装置による造形受託業務を始めるべく、株式会社アスペクトは誕生した。オバマの一般教書より17年も前の1996年のことだった。
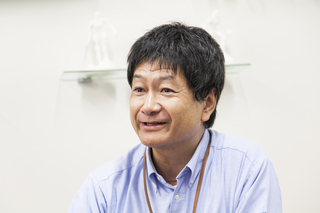
ピンチをチャンスに変えた、自社装置開発
PBF技術を用いた3Dプリンターの輸入販売と造形受託業務をスタートさせたものの、PBF技術の黎明期だっただけに、装置の故障は少なくなかった。販売元はアメリカ、日本に支社もなく、修理がままならなかった。メンテナンス要員として萩原さんに声が掛かった。光造形装置の開発に携わっていた腕を見込まれてのことだった。技術の将来性を見込んで萩原さんは快諾。これで保守環境が整ったと思った矢先、まさに青天の霹靂といえる出来事があった。
「販売元がアメリカの大手3Dプリンターメーカーに買収されて、その後、販売権の打ち切りを告げられたんです。それまで6000万円ほどするプリンターを40台前後は販売していましたから、日本は良いマーケットになると買収先が踏んで、自分たちでやったほうが儲かると考えたのでしょう」(萩原さん)
生命線を絶たれたかのような宣告であったが、萩原さんはこれを好機と見た。自社装置の開発に乗り出したのである。
「ゆくゆくは自社装置を開発しようと思っていましたから、それが思ったより早くなっただけのことです。輸入代理店をしていたらビジネスマナーに反するので開発はできませんからね。もっと良い装置を作ってやると燃えていましたよ」
萩原さんが目指したのは500mmサイズの造形品を作れる3Dプリンター。輸入していたものは300mmサイズでしかなかった。
「500mmにしたのは自動車部品を想定していたからです。例えばガソリンと空気を混ぜて燃焼室に送り込む経路になるインテークマニホールドという自動車部品があります。自動車メーカーからこの部品の製造を発注してもらうには、部品製造会社は、試作品を提示する必要があるんです。そこで弊社に依頼が舞い込んでいたのですが、300mmサイズだとまず半分のものを作ってそれを接合しなければならなかったんです。こうした手間を省くために大きなサイズを作れるようにしようと考えました」
チャレンジ精神旺盛の萩原さん、光造形装置のノウハウとPBF装置のメンテナンス経験はあったものの、レーザーの種類やモーターのスピード、あるいは機械部品に使用する金属など、学ばなければならないことが山積していた。まさに一からの設計で、完成したのは2006年、実に3年を要した。現在ではさらに生産性を向上させた新作機も完成している。研究はまさに日進月歩だと萩原さんは話す。
「現在では3Dプリンターの開発のみならず、粉末に使う新素材の開発や既存材料の3Dプリンターへの適合化などに取り組んでいます」
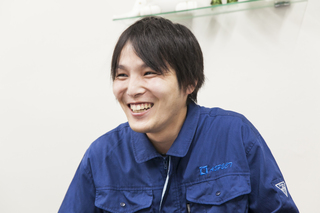
若手がものづくりの未来を変える
同社の肝といえる研究開発には若手社員も携わっている。
「現在、3Dプリンターで使用される素材でポピュラーなものはナイロンですが、私が今研究しているのはポリプロピレンです。ポリプロピレンは汎用性が高くコップやペットボトルのキャップなど、その例をあげたらきりがないほどです。この素材が3Dプリンターで使えるようになれば、3Dプリンターのマーケットはさらに拡大するに違いありません」(木村友星さん 入社2年目)
温度が高ければうまく凝固せず、低すぎてもプラスチックが反り返ってしまう。研究は実験と観察の繰り返しだという。同じようにナイロン以外の素材での造形に取り組んでいるのが入社2年目の小清水秀和さんだ。
「ステンレスの粉での造形に挑戦しています。プラスチックとは違ってノウハウが蓄積されていないので、層がバラバラになってしまったりして、まったくうまくいかないこともありますが、自分が予想した通りの反応が出ることもあるので、それがやりがいになっています」
これまでの造形法とは異なったやり方にチャレンジしている社員もいる。入社2年目の伊藤史郎さんは東京大学の生産技術研究所に出向し低温造形法という新たな成形法の研究をしている。
「プラスチックの中でも融点が高い素材があります。例えばPPSという素材は融点が約280度なので、通常のやり方で融かそうとすると装置自体の耐熱性を上げなければなりません。そこで、低温でゆっくり融かす低温造形法を研究しています。ただし、低温だと反り返ってしまうので、足場を作ってそこに層を固定して、その上に層をどんどん積み重ねていくんです。現在は足場の作り方やレーザーの強さの最適化などに取り組んでいます」
いずれの研究も成功すれば新たなマーケットが開けることになる。自分の研究がものづくりの業界を変えていく。そのことがやりがいになっているとともに、同社が成長を続けている原動力になっているに違いない。
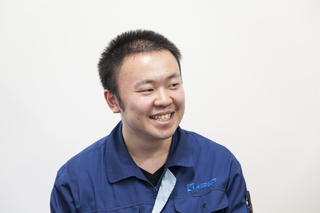
編集部からのメッセージ
真空状態で行われる金属造形
同社の金属粉末による造形は、真空状態の中で行われる。空気による酸化を防ぐためである。また、金属には結露しやすいという性質があるため、水分などの不純物が混入しやすく、品質劣化を招く恐れがある。その不純物を除くにも、真空が好条件になるのだという。この研究に取り組んでいる小清水さんは面白さをこう話す。「研究は、金属造形機のレーザーの強さや照射の仕方などをチューニングし、造形、その結果の観察という繰り返しです。一見単調に見えますが、1回1回結果が違うので、なぜこの形になったのか、次はもっと細かくレーザーを当ててみようとか、考察すべきことがたくさんあるんですね。そうしたことを考えること自体も面白いですし、どんな結果になるのかというワクワク感もあるんですよ。それに真空状態による金属造形は宇宙開発業界からも注目されているので、それもやりがいになっています」。なるほど、最先端技術に携われるというやりがいと研究自体の面白さが働く上でのモチベーションになっているというわけだ。まさに働きがいたっぷりの職場環境といえよう。
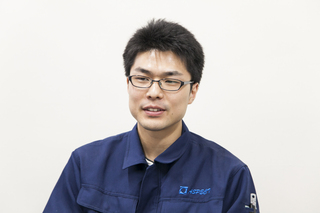
- 社名:株式会社アスペクト
- 設立年・創業年:設立年1996年
- 資本金:3,000万円
- 代表者名:代表取締役 早野誠治
- 従業員数:40名(内、女性従業員数10名)
- 所在地:206-0802 東京都稲城市東長沼 3104-1-101
- TEL:042-370-7900
- URL:http://aspect.jpn.com/
- 採用情報:こちらからご確認ください。