株式会社本間製作所
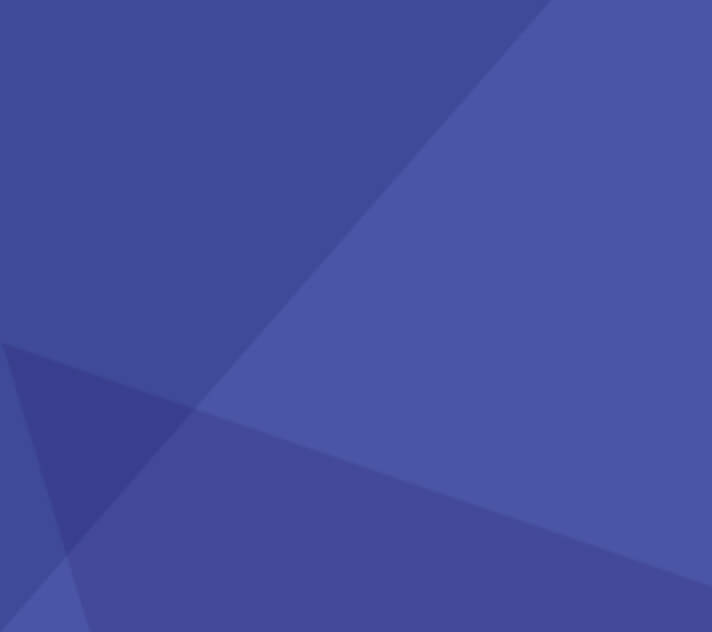
株式会社本間製作所
70年の歴史を誇る金型メーカーが目指す“自社製品メーカー”という新たな柱
ミクロン単位の加工技術力を武器にする金型メーカーが生み出した、職人の技を再現する高精度位置決め治具
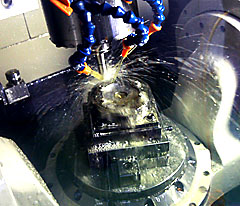
株式会社本間製作所
70年の歴史を誇る金型メーカーが目指す“自社製品メーカー”という新たな柱 ミクロン単位の加工技術力を武器にする金型メーカーが生み出した、職人の技を再現する高精度位置決め治具
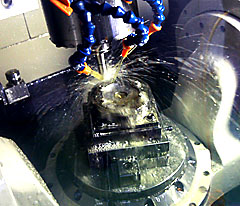
- 社名:株式会社本間製作所
- 設立年月:1941年
- 資本金:7500万円
- 従業員数:60名
- 代表者:代表取締役社長 本間 聖敏
- 社員平均年齢:-
- 初任給:-
- 主な勤務地:熊谷工場
- 休日:110日
- 本社所在地:東京都北区赤羽西1丁目6番1号
- 電話番号:048(532)6551
- 公式HP:http://www.honma-k.co.jp/
- 「技術力のある金型メーカー」という現状に安住せず、新たな事業の柱として自社製品の開発・製造に乗り出し、そのチャレンジを着実に成功させつつあるのが株式会社本間製作所だ。ミクロン単位で加工する職人の技を誰にでも再現できるようにするその製品によって、今まで面識のなかった大企業とも縁が生まれ、本業である金型製作の方にも好影響が及んできている。
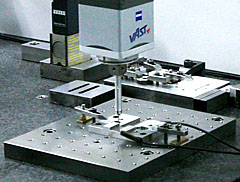
事業紹介
【精密治具・高機能部品】
製品事例
■HDD用サーボライタ装置(メディア書き込み装置)
HDDのメディアへの書き込みをする装置の心臓部であるキャリッジ部の製作
■HDD用サスペンションレーザー溶接治具
サスペンションをレーザー溶接する際、位置決め精度を必要とする治具の製
■HDD用駆動コイルアームASSY一体モールド成形金型
入れ子駒組構造を採用・入れ子の互換性は良好
■HDD用ボンディング治具
HDDヘッド部(ディスク読み取り部)のチップを装着する治具の製作
■半導体、液晶パネル製造用治具
液晶注入・封孔・FPD検査
【射出成形金型・粉末成形金型】
製品事例
■フェライトマグネット用金型
自動車・家電製品
■希土類マグネット用金型
リニア・電気自動車モーター・サーボモータ・自動車・電装品
HDDスピンドルモーター・センサ・CD-ROMピックアップ
■プラスチック用射出成形金型
携帯テープレコーダー試作
■プラスチックマグネット用射出成形金型
【食品・医療用金型】
製品事例
■打抜きプレス
・充填シール機用
ギフトデザート(プリン、水羊羹)、ベビーフードなどの樹脂容器、アルミニウム箔容器、ポーションカップ、豆腐容器
・フィルム製袋機用
スパウト付パウチ(飲料水・食品用 等)、詰め替え用パウチ(洗剤 等)、ナイロン製食品袋(インライン自動機用)、食品包装袋、医薬品用バッグ
■成形金型
製袋用コーナーカット、打抜ヒートシール、ノッチカッター、スリット刃、丸角変形パンチ、シールヘッド、ミシン刃、ギザカッター、ダブテープカッター、ストレート刃 等、 ブリスター包装打抜ダイセット(歯ブラシケース等)、真空圧空成形金型、製袋用シール型、熱成形型、製袋用エンポス金型、製袋用冷却金型
エコカーやハードディスクで使われるマグネットを生み出す粉末成形金型
株式会社本間製作所は、1941年の設立以来、金型を作り続けてきた老舗メーカー。特に金属粉末を固めて成形するのに使う金型を扱っていて、その金型からは主にモーターなどに使われるマグネットが生み出されている。 「本間製作所は、自動車関係で使われるフェライトマグネット、発電機などの駆動制御に必要な希土類マグネットの金型でかなりのシェアを持っています。今は、電気自動車やハイブリッドカー、家電などにも使われるハードディスクの出荷が伸びていますから、希土類マグネットの市場が拡大している状況です」と同社代表取締役社長の本間聖敏氏。売れ筋の電気自動車やハイブリッドカーにはかなりの数の希土類マグネットが使われているが、その基盤になっているのが同社の金型だと本間氏は言う。 日本のモノづくりの海外流出が懸念されているが、「私たちの金型は、工作機械にCADデータを入れただけでは作り込めない。海外ではまねできない製品です」と本間氏は熱を込めて話す。粉末成形の金型には、極めて高い精度が必要。そのために本間製作所ではマシニングセンタ、ワイヤー放電加工機、工具研磨機、円筒研削盤、NCプロファイルなどの工作機械を導入して、同社の中だけで全工程を手掛けられるようにした。工程ごとに念入りにチェックすることで品質・納期・価格で他社に負けないように努力している。特にミクロン単位の加工技術が要求される最終工程の合わせ加工には自信を持っており、加工を根気強く続けられる日本人の国民性が何よりの武器になっていると本間氏は誇っている。
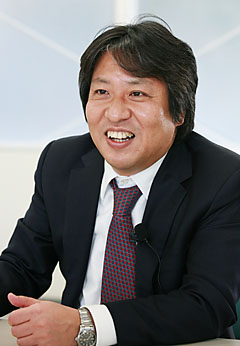
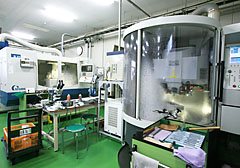
職人の技を治具で再現できる自社製品「ホンママルチチャック」
そのように金型のメーカーとして事業展開してきた本間製作所が、初めての自社製品として世に送り出したのが高精度位置決め治具の「ホンママルチチャック」。熟練技術者の技を誰にでも再現できるようにしようと開発した製品で、ホンママルチチャックを使って位置決めをすることで、2ミクロン以内の精度での加工が可能になる。 「職人の技を治具で再現できるようにすることが一番のポイントです。今までは職人が休むと、担当工程が動きませんでした。多くの中小企業がこの問題に悩んでいたと思うのですが、ホンママルチチャックを使えば、誰にでも加工できるようになります。職人の技術を治具へと置き換えていく。そんな狙いを持って開発しました」(本間氏) ホンママルチチャックに対する反響は大きく、さまざまな媒体から取材を受けた。東京都トライアル発注認定制度からの認定も受け、板橋製品技術大賞で最優秀賞を受賞。導入企業数も着実に増えてきている。 「大手企業での導入実績も出てきています。なかなか大手企業とは新規取引できないものですが、ホンママルチチャックがきっかけになって面識を持てるようになり、大手企業から金型などの依頼も来るようになってきました。実は、そうしたプラスアルファの効果も狙っているのです」(本間氏)
自社製品メーカーへのチャレンジを助け、一緒に会社を大きくしてほしい
金型メーカーとして70年の歴史はあるが、自社製品を開発するようになってまだ3年しか経っていない。本間氏は「自社製品メーカーとしては、本当に最初の一歩を踏み出したばかりでまだ弱小です。弱小メーカーがブランド力のある企業になれるよう、一歩一歩、力強く踏み出していきたい」と今後について見据えている。 ホンママルチチャックの成功に満足せず、これからも世の中に存在していない、みんなが困っていることを解決できる製品を開発していきたいと本間氏は言う。そのために必要なのは、そのチャレンジを手助けしてくれる人材。同じ思いを持ってくれる若い人材と一緒に、本間製作所を大きくしていきたいと本間氏は考えている。 「新しいことにチャレンジするのに必要な考え方というのは、歳を重ねることで薄れてしまうところがあります。いろいろなことを勉強して知識を身に付けてしまうと、柔軟な発想は出にくくなってしまうものです。 ですから、先入観にとらわれない若い人たちの発想がプラスになる可能性は大いにあります。モノづくりについて詳しくなくても、『こういうやり方があると便利ですよね』『こういう製品が市場で受け入れられるのではないでしょうか』と考えられる力があれば、あとは技術力を持った本間製作所の先輩社員が形にしてくれます。市場が求めているものを的確につかんで、本間製作所のチャレンジを手助けしてくれる人材を当社では求めています」(本間氏)
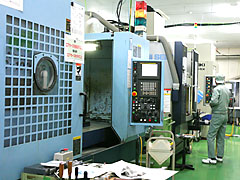
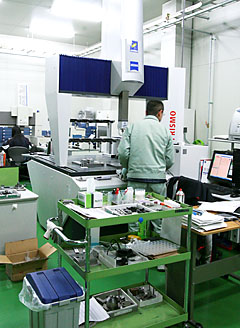
先輩メッセージ
寸法どおりに仕上がった時の達成感は、加工した本人でないと分からない
製造部 副部長
武田さん
――副部長として、どのような役割を担っていらっしゃるのですか?
当社は部長2人と副部長の私1人の3人で製造業務を見ていまして、私は特にマシニング加工の部門を担当しています。
3人で情報交換をしながら、納期を確認して遅延が発生しそうな時には、いち早く対策をするといった役割を担っています。
教育・指導も重要な役割です。自分の培ってきた技術を伝授するために、基本的にはOJTで教えています。多能工を増やすことが目下の課題ですね。あとは改善提案を出しやすくする雰囲気作りをして、部下の持っている魅力をどんどん出せるように心を砕いています。
――貴社での働きがいは、どういうところにあるとお考えですか?
図面に従って材料を加工して、図面どおりのものができた時の喜びに勝るものはないでしょう。
モノづくりの一番の魅力は、完成品を自分の目で見られることだと思っていますが、当社の製品は金型です。あいにく最終製品ではありませんが、それでも図面どおりにミクロン単位の加工ができると感激ものですよね。当社にはさまざまな機械があり、その中でも加工が難しい機械を使って、寸法どおりの仕上がりができた時の達成感は、加工した本人でないと分からないと思います。
――ホンママルチチャックという高精度位置決め治具の自社製品をお持ちと伺いました。実際、業務の中でも使われているのですか?
かなりの数を使っています。誰が使ってもしっかりと位置決めができますから、非常に役立っています。
技術者が1人前になるまで3〜5年はかかるところ、ホンママルチチャックを使えば、清掃して取り付けるだけで済みますから1年目からできてしまいます。
ただ、新しい加工をやる時には、段取りから始めなくてはいけませんから、そこは加工に関するノウハウが必要になります。加工内容を確認しながら、材料はアルミなのか鉄なのか、いろいろな条件に合わせて最適な選択をしなくてはいけません。そういったところは、教えていかないといけないところでしょう。
――現場で求める人材像について、お聞かせいただけないでしょうか。
製造業なら、どの会社でも同じだと思いますが、やはりやる気のある人間、ガッツのある人間、あとは周りと仲良くして和を保ちながら仕事のできる人間、会社の事情を分かってくれて協力的な人間ということになるでしょうか。
いろいろな知識を持つ人材が評価されるところは確かにありますが、一から丁寧に指導して1人前に育てていきますので、何より途中で退職されてしまうことを一番避けたいのです。だからやる気があって、ガッツがあって、周りと仲良くできることが、大切な資質になると感じています。
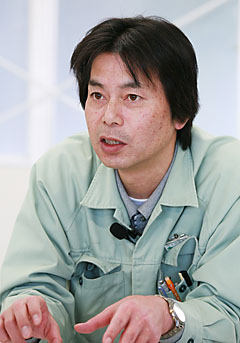
同じ加工は滅多になく、常に新しいものに切り替わっていくところがおもしろい
製造部
腰塚さん
――本間製作所への入社を希望するようになったのは、なぜですか?
私は工業高校で学んでいまして、そのころは自動車の整備士を目指していました。けれど、就職活動中に本間製作所を見学する機会がありまして、その時に目にしたワイヤー放電加工機に興味を持ちました。
工業高校にはワイヤー加工機はありませんでしたから、どういう仕組みで動いているのか、まったく分かりませんでした。完全に興味本位で、この機械についてもっと知りたいと思ったのが志望理由です。
――ワイヤー加工機とは、それほど珍しい機械なのでしょうか。
ワイヤー加工機を所有している会社の数自体、少ないですね。それに加えて、本間製作所は特に保有台数が多かったのです。
――入社後、希望していたワイヤー加工機を操作する機会は得られましたか?
はい。最初からワイヤー加工機の担当になれまして、その後、ほかの機械を少しずつ経験しています。今はワイヤー加工機のほかに、細穴加工機も使うようになっています。
――仕事は、どのように覚えていったのですか?
まずはワイヤー加工機用のプログラムの作成から覚えていって、その後、機械加工について学んでいきました。
当社ではプログラムと機械加工を少しずつ両方触りながら覚えていきます。私の場合、工業高校でCADを使えるようになっていましたので、プログラム関連はそれほど時間がかかりませんでした。最初から機械加工のやり方を覚えていく方に重点を置いて教わりました。
――ワイヤー加工機を実際に使ってみて、感想は?
おもしろいですね。入社してそろそろ7年になりますが、それでも飽きません。
金型は毎回、違う加工になりますから、プログラムを修正しないと完成しません。同じものを作ることは滅多になく、常に新しいものに切り替わっていきます。そこがおもしろいですね。
――今、ご自身で目標とされていることを教えてください。
今の目標としては、自分の担当する製品を段取る時間が上司と比べると少し遅いので、もっと早くできるようになりたいです。その上で、もっと精度も上げていきたいです。
あとは2人の上司に任せっきりになっている部分がありますので、自分でできるように技術力を磨いて、そこの負担を減らせるようにしていかないといけませんね。
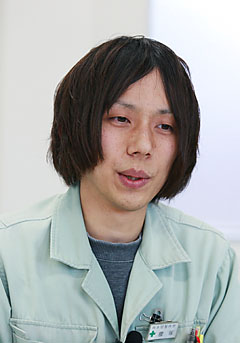