株式会社井上製作所
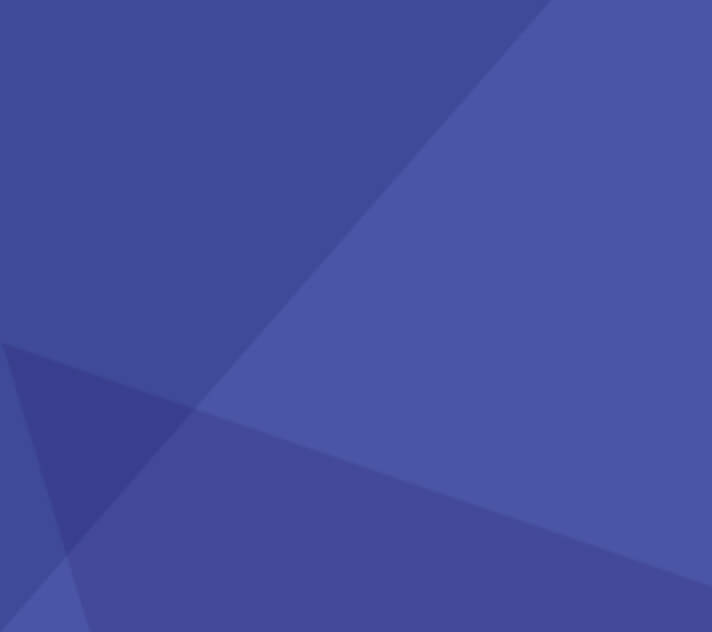
株式会社井上製作所
日本の半導体メーカーを40年以上支え続ける大田区のモノづくり企業
数百社という外注先を抱える大手企業からも頼りにされる職人の技
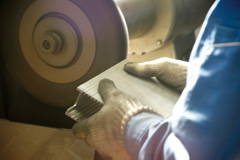
株式会社井上製作所
日本の半導体メーカーを40年以上支え続ける大田区のモノづくり企業 数百社という外注先を抱える大手企業からも頼りにされる職人の技
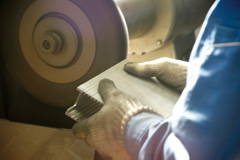
- 社名:株式会社井上製作所
- 設立年月:1966年4月
- 資本金:1000万円
- 従業員数:20名
- 代表者:代表取締役 井上 健太郎
- 本社所在地:東京都大田区城南島2-1-3
- 電話番号:03-3790-0521
- 公式HP:http://www.inoue-ss.co.jp/
- 日本のモノづくりを支える中小企業が特に集まっていることで有名な東京都大田区。株式会社井上製作所も半導体製造に欠かせない治工具の製造を40年以上も続けてきた。20代〜30代前半の社員も多く働いている同社では、社員に働きがいを感じてもらえるように、朝礼で改善提案をする場を用意。治工具という目に付きにくい製品をつくっている分、普段の業務の中でやりがいを感じられる環境を整えている。

事業紹介
株式会社井上製作所では昭和41年創業以来、金属加工一筋に研鑽を重ねて参りました。
長年にわたり蓄積いたしましたノウハウはお客様より高く評価を頂いております。
常に品質の向上に挑戦し続け、お客様第一の姿勢でご要望にお応えできる体制を確立しています。
半導体製造用の治工具で40年以上研鑽を重ねた井上製作所
「企業も人も運がある。オイルショック、バブル崩壊、ITバブル崩壊という出来事があった中で乗り切ってこられたのは、半導体メーカー・商社・金属メーカーと井上製作所との四角形のきずながあったのと、半導体製造に限界が見えるたびにLEDなどの新しい半導体が登場してきたからでしょう」。株式会社井上製作所の井上忠道代表取締役は、1966年から続く同社の歴史についてこのように振り返る。 井上製作所はやアルミニウムの押出型材の精密加工を得意とする。主に半導体製造用の治工具を製造、約40年間にわたって売上の7割ほどを占めてきた。 井上氏が語る四角形のきずなとは、半導体メーカーが製造を始める際、まず商社に依頼をし、商社が金属メーカーに素材を頼み、金属メーカーから井上製作所に金属素材を入荷し加工、という一連の流れのこと。40年間にわたってこの関係は一切揺るがず、信頼関係によって結び付いてきた。さらに言うなら、一種のきずなのようなものさえ芽生えているのだという。
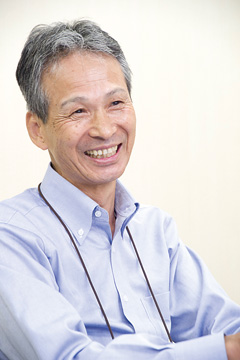
コンマミリ単位の精度が求められる半導体関連の治工具製造
井上製作所では、半導体のリードフレームを収納するマガジンなどを製作している。リードフレームとは、半導体チップを固定して外部配線との橋渡し役を務める基盤部品。半導体生産の規格に対応することになるため、コンマ何ミリ単位の極めて高い精度で、図面どおりに製作することが求められる。 「弊社は、リードフレーム用のマガジン供給量では日本で1番でしょう。金属メーカーが押出したアルミ型材を寸法どおりに加工するには、通常の加工技術では無理です。私どもはお客様の要求水準を満たせるように、工夫を積み重ねて、最後のところは職人の技でお客様の希望に合うように矯正しています。 お客様の希望を満たすのは、技術的には難問ですが、お客様に育てていただいたと言えるかもしれません。要望に対して確実に応えてきたからこそ、井上製作所も含めて『大田区の中小企業はすごいね』という評判を得られたのでしょう」(井上氏) 半導体業界で培われた井上製作所の技術力は折り紙つき。つい最近も、大手の照明器具メーカーから「どこに依頼してもできないから頼めないか」と依頼を受けた。そのメーカーには何百社と外注先があった中、依頼内容を達成できたのは井上製作所だけだったそうだ。 それほど高い技術力を持ちながらも、井上製作所には製作した製品がどこで使われているかが分かりづらいという悩みがある。お客様の工場の製造工程で使われる製品を手掛けているため、「これをつくったんだ」という実感を得られにくいのだという。 「つくったものが見えないところで使われているから、モチベーションを上げることが難しくなっています。ですから、加工に30分掛かっていた作業を20分に短縮できたとか、作業を改善していく取り組みを評価するようにしています。改善提案を朝礼で発表させて、意識を高めていく。自分たちの仕事の成果を発表する場を用意できるように心掛けています。 モチベーションを上げるもう一つの解決策は、お客様に喜んでいただくことでしょう。自分が責任を持ってつくったものがお客様に喜んでいただけるということが私どもには一番の発奮材料になりますから」(井上氏)
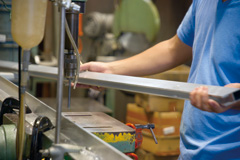
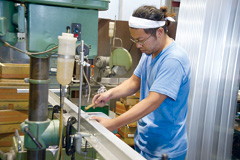
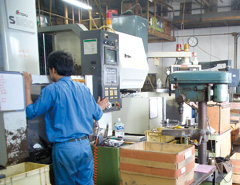
円高で厳しい環境の中、次世代への代替わりをどう進めるか
40年以上も半導体関連の治工具を製作してきた井上製作所だが、井上氏は最近の行き過ぎた円高に危機感を抱いているようだ。 「『日本でモノづくりを続けていても仕方ない』とテレビでは言われています。このまま円高が続くと私どものような企業はきっと市場の中で埋没していってしまうでしょう。それに対して、どうしていけば良いのか。海外のメーカーと組むようなことを真剣に考えていかないといけないでしょう。 ただ、私どものような小さな会社が闇雲に冒険をするというのは大変難しいことです。それだけで経営を傾かせてしまうことにもなりかねません。どういう展望を描きながら、次世代に引き継いでいくのか私もある程度の具体的なことは話をしています。 最近の円高で日本のモノづくり企業は苦境に立たされていますが、日本を代表するメーカーの中でも日本に製造拠点を残して頑張ると表明する会社も出てきています。そういう大企業が覚悟を固めてくれるのなら、まだまだ中小企業も生きていけるでしょう」
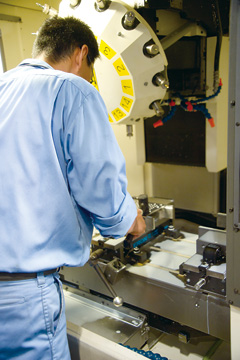
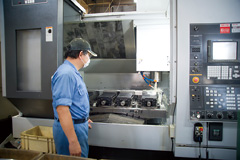
先輩メッセージ
求められるのは加工の精度と治具・工具の使いやすさ
第一セクション セクションマネージャー先城(せんじょう)さん
――担当されている業務内容は?
私の部署ではNC制御工作機械で半導体メーカー用の治工具の製作を行っております。私はその中で、CAD/CAMを担当しています。図面を新規に引いたり、治工具を使うお客様から参考図面をいただいて、当社で製作できるように図面を修正したりしています。
お客様からは、加工の精度を求められます。あとは使いやすさも重視されます。図面を引く前には、お客様が治工具をどう使いたいのか話を聞いて、加工する工程を思い浮かべながら図面にします。
――これまでの仕事で印象に残っているものは?
自動車メーカーから依頼でボディ用のアルミパーツを作ったことがありました。当社にとっては大きな部品で、加工用の治具から設計しました。これまでの仕事の中で一番印象に残っています。
大型の部品はねじれが生じすいため、精度が出ません。治具を工夫して、カーブをつけたり押さえ方を変えてみたりして、ねじれが出ないように試行錯誤を重ねました。
――仕事に取り組んでいて、やりがいを感じる瞬間は?
お客様から「期待以上のものができた」「貴社に頼んで良かったよ」とお褒めの言葉をいただくと一番やりがいを感じます。
お客様が見込んでいたよりも早く納品出来たり、当社独自のノウハウを活かして図面を作成し、期待以上の仕上がりで納めると喜んでいただけるので、そうした工夫ができるように心掛けています。
――今後の抱負について教えてください。
加工技術のレベルの引き上げですね。当社は3軸加工までは対応できますが、4軸や5軸の加工は難しくなります。さらに高度な加工技術にもどんどん挑戦して行くために現在準備を進めています。
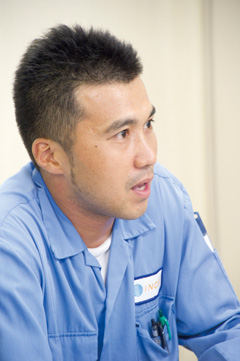
先輩メッセージ
工程を工夫して1日2時間掛かっていた作業を改善
第三セクション マシニンググループ長谷川さん
――入社するまでの経緯を教えてください。
入社したきっかけは、当社の中途採用の求人情報を見たことです。中途の経験者募集でしたが、未経験だった私は思い切って飛び込んでみました。それまでのアルバイトで引越しの手伝いやファミリーレストランでの調理の仕事をしたことがありましたが、手に職をつけたいという気持ちが強かったのです。
工場と言えば、汚くて、年配の工員しかいないという先入観を持っていました。ですが工場に行って見たら、実際の工場が先入観とは違うことがよく分かりました。整理整頓されていてきれいでしたし、職場の雰囲気も活気があり明るくて、年齢が近い先輩たちもいる。「この工場だったら働いていけるのかな」と感じて、入社を決めました。
――現在のお仕事は?
ヒートシンクという放熱用部品の製造を任されていまして、機械加工・製品洗浄・出荷という全工程を担当しています。
当社では社内での作業工程を改善する取り組みが朝礼で紹介されます。自分なりに工夫してできた改善事案を発表するときはとても達成感が得られ積極的に取り組んでいます。
例えば、製造の工程が終わってから、部品が仕様どおりにできているかを、ノギスという測定器を使って全品検査していました。1日当たり2時間は掛かっていたでしょうか。それをエンドミルという切削工具を使って、完成品のサイズが仕様よりも大きかったらエンドミルの刃が当たるように加工工程を工夫しました。そうすることで、1日に2時間掛けていた全品検査が要らなくなり、一つの工程の中で検査もできるようになりました。
――今後の目標をどうぞ。
スキルアップしていきたいです。特にCAD/CAMを勉強して、いつか新入社員が入ってきたときに、指導・教育できるくらいに早くなりたいですね。
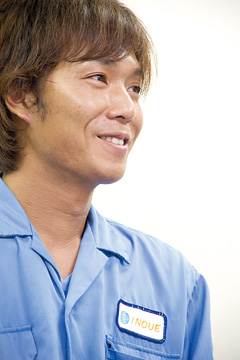