株式会社 加藤研磨製作所
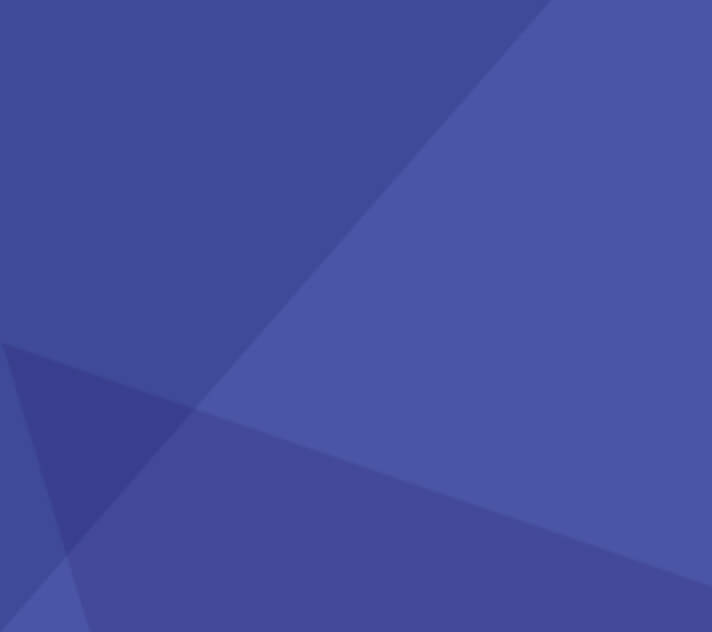
株式会社 加藤研磨製作所
重要部品を誤差±1000分の2ミリ以内に精密加工
約2000種類の砥石を使い分け、重要な部品を1000分の1ミリ単位で精密加工する技術者集団
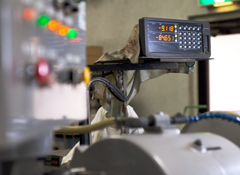
株式会社 加藤研磨製作所
重要部品を誤差±1000分の2ミリ以内に精密加工 約2000種類の砥石を使い分け、重要な部品を1000分の1ミリ単位で精密加工する技術者集団
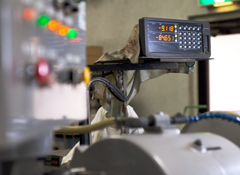
- 社名:株式会社 加藤研磨製作所
- 設立年月:1954年10月
- 資本金:700万円
- 従業員数:45名
- 代表者:代表取締役社長 加藤 義弘
- 主な勤務地:大田区西糀谷(京急蒲田駅より徒歩15分 バイクによる通勤可)
- 休日:当社カレンダーによる週休2日制 GW・夏季・年末年始休暇あり
有給休暇(2015年実績 103日) - 本社所在地:東京都大田区西糀谷2-7-3
- 電話番号:03-3745-6321
- 公式HP:http://www.kato-kenma.com/
- ・1000分の1ミリ単位で部品を研削して仕上げる技術者集団
- ・研削だけでなく切削・めっきなどの全工程を扱える一貫生産体制
- ・ベテラン、中堅、若手のバランスが良い年齢構成で溶け込みやすい職場
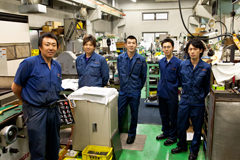
事業紹介
加藤研磨製作所では、平面研削・円筒研削・内面研削・治具研削・プロファイル研削等の各種研削加工を中心とした、精密部品製作を行っております。
金型部品や産業機械・工作機械等の部品、その他、各種ガイドブッシュ・ガイドピン・スピンドル・アーバー・シャフト、治工具、試作部品等、図面1枚で1ヶから受注、製作をさせて頂きます。
何を作ってる?
プレス金型用部品や、寸法を計測するのに使うゲージ、製造装置内の重要な部品といった精密部品を手掛けている。 加藤研磨製作所に依頼が来るのは、高い精度で寸法どおりに仕上げる必要がある多品種少量の部品ばかり。砥石が付いた研削盤で研いて削る研削技術を使い、1000分の1ミリ単位で部品を加工。どんな依頼であっても、指定された寸法に対して、誤差±1000分の2ミリ以内に必ず仕上げて納品している。 同社が保有する研削盤は10種類以上約40台。研削盤で使う砥石は約2000種類。加工する寸法や金属の材質、仕上がり面の輝きに応じて、研削盤や砥石を使い分けている。 これだけの数、種類の研削盤を持っている企業は関東全域を見渡してみても五指に満たないほど。代表取締役社長の加藤義弘氏は自社の研削技術について、「部品の大きさによっても違うので一概に比べることはできませんが、寸法どおりに高い精度で仕上げる技術力については、日本の中でも上位に位置していると思います」と自負している。
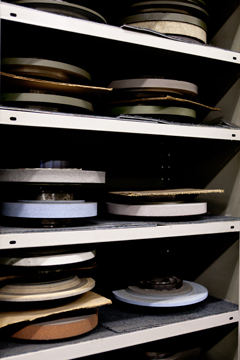
会社の強み
1000分の1ミリ単位で加工できる研削技術に加えて、図面さえあれば材料の手配からめっきを掛けて検査・出荷するところまで、一貫して生産できる体制を10年ほど前から徐々に整えてきた。 依頼主の立場から考えると、切削・研削・めっきといった工程ごとに発注先の企業を変えていては、作業の進み具合を管理する手間や時間が都度掛かってしまう。もし一貫生産で希望どおりの部品を仕上げてくれる企業があれば、依頼主側の手間を省ける。そして加工を任される加藤研磨製作所にとっては、自社で全工程を行うことで、より短い期間で納品できるようになる。 同社がすべての工程に対応できるようになったことで、取引先企業からの評判はさらに高くなった。依頼される仕事の量も明らかに増えてきたと加藤氏は手応えを感じている。
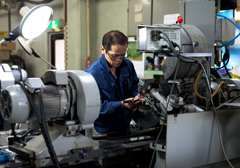
職場としての魅力
加工する部品は、金型や製造装置など、モノづくりの上流で使われるものが多い。上流でわずかでも誤差があると、先に進むに従って誤差はより大きなものへと広がっていってしまう。高い精度で寸法どおりに仕上げることで、「加藤研磨製作所さんの仕事が良かったので、最終製品のできあがりが良くなりました」と取引先企業から感謝されることが何よりの励みになる。 また、高い技術力を持つベテラン社員だけでなく、30~40代の中堅社員、20代の若手社員と年齢構成のバランスが良い。「熟練社員は、新入社員が仕事のどこでつまずいているのかが分からない。仕事を最近覚えた若手が教えることで、すんなりと技術を覚えられるはず」(加藤氏)と考え、新入社員にはまず5~10年目の若手社員が教える体制にしている。若手社員にとっては教えることで技術への理解を一層深め、新入社員にとっては年齢が近い先輩と一緒に働くことで職場に溶け込みやすくなるというメリットがある。
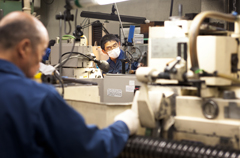
社長メッセージ
主軸になる研削加工に資源を集中し、今以上に技術力を高めていきたい
代表取締役社長
加藤義弘さん
――経営者として心掛けている点について教えてください。
当社は創業から58年が経ち、私が3代目の社長です。この歴史を受け継いで、会社がずっと存続できるようにしたいと考えています。
製造業の仕事が日本から海外に移り、空洞化が進んできています。ですが、日本でしかできない高度な仕事は確かにあります。生き残るには、そこに特化していくことです。
当社の主軸となる技術は研削加工です。そこに資源を集中して今以上に技術力を高めることで、世の中全体の仕事量が減ったとしても、当社に来る仕事量は減らないような状態にしたいのです。売上規模や利益を追求するよりも、とにかく会社が残っていけるよう模索しています。
会社が潰れてしまっては、せっかく若い人が入社して技術を身に付けてくれても、役立てるところがなくなってしまいます。入社してくれた社員がずっと当社で働き続けられるようにすることが第一だと感じています。
ですから、当社で技術を長期間にわたって磨き上げて、仕事に役立てたいという方に入社してほしいと思っています。
みんな非常にまじめで、仕事に一生懸命取り組んでくれていると私は感じています。苦しい就職活動を乗り越えてきただけに、前向きな気持ちで仕事に取り組んでもらえているのではないでしょうか。
若い人には期待していますから、当社では技術力を身に付けた社員には相応の昇給や待遇を用意し、努力した人が昇給する体制にしています。
反面、実力主義なので、技術が追いつかないと辛い仕事になるかもしれません。でも、努力した人には必ず後から結果がついてくるものです。結果が出始めれば仕事へのやる気も出るでしょうし、会社もずっと発展していけるのではないかと考えています。
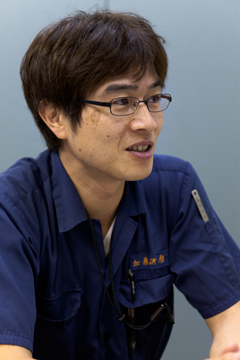
先輩メッセージ
百聞は一見にしかず。まずは会社や工場を見学することが大切
製造部
窪田さん
――加藤研磨製作所のことを知ったきっかけは何だったのでしょうか。
就職活動中、東京しごとセンターへ相談に行ったら、「中小企業が参加する就職セミナーがあるから行ってみないか」と勧められました。何の気なしに行ってみたら、加藤研磨製作所が出展していたのです。
モノづくりに携わっていたわけではないので何も分からなかったのですが、「自分で何か作れる仕事は悪くないな」と感じました。社員の方からも「何も分からないのなら、ぜひ会社を見学してみてほしい」とお誘いただきまして、見学してみることにしました。
「1000分の1ミリ単位で加工をしていて、花粉よりも小さな単位の世界になる」と説明を受けましたが、正直、最初は何を言っているのかもさっぱり分からないくらいでしたね。ただ、ものすごいことをやっていると感じましたので、面接を受けることにしました。
最初のうちは、工場向け大型クーラーの製造装置に使われる部品を削る仕事をしていました。
決められた寸法に近づけていくのは簡単でしたが、計測することが難しかったです。部品に触れている指の温度が伝わるだけでも、1000分の1~2ミリほど大きさが変わってしまいます。
1カ月ほど続けていたら、100分の1ミリくらいの違いは気付くようになりました。今は仕上げ寸法よりも手前のところ、1000分の5ミリくらいの精度で粗削りし、先輩に仕上げをお願いするようにしています。
今でも忘れられないのは、4本しかない部品の加工でミスをしてしまったことですね。1本もミスが許されない状況だったのですが、私がミスをしたらすぐに先輩が挽回してくれました。一貫生産をやっている社内の別の現場に依頼して、ミスする前の寸法の部品を大急ぎで用意してくれたのです。
ほかにも、社内で使う治具やゲージはすべて社内で作っています。中にはかなり大きなサイズのものもありますから、先輩たちの技術力には驚かされますね。
金属を削ると銀色の光沢が出るのですが、きれいに削ることができれば輝きが違うことに一目で気付きます。自分の力できれいに削れたことがあって、先輩から「すごくきれいに削れたな」とほめていただいたことがあります。うれしかったですね。
あとは仕事をしていると、あいまいなところがなく、作業に掛かった作業時間から円筒状の部品の径の寸法まで、すべて数字として残ります。自分の仕事が会社の求める数字の範囲内でできていると、楽しいです。
当社では、手で持てないくらいの大きさの部品も扱っています。それほど大きな部品であっても、1000分の1ミリ単位で加工しなくてはいけません。大きな分、温度によるサイズ変化も大きくなりますので難しい仕事になります。いつかはそんな仕事を任せてもらえるようになりたいと思っています。
これから就職活動をする人は、Webや情報誌で情報を調べてみるだけではなく、まずは会社や工場を見学してみることが大切だと思いますね。見てみないと分からないことが多いですから。
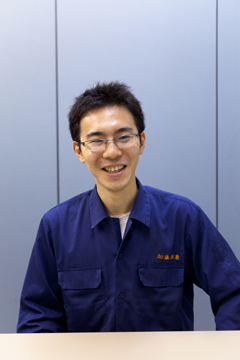
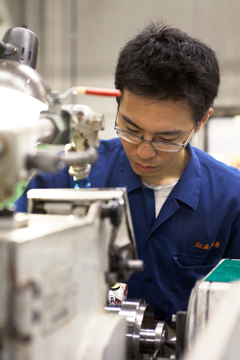
先輩メッセージ
「大田区で作られた部品をNASAが採用」との報道を見て、モノづくりを志すように
製造部
橋本さん
――どのような就職活動を送られたのか、教えてください。
私は大田区の出身です。モノづくりをしている町工場が身近にあって、テレビで「大田区の町工場が作った部品をNASAが使っている」と報道されるのを見ていましたから、「モノづくりはかっこいいな」と憧れていました。
就職先としてモノづくりの企業を探していましたが、私のような未経験者を受け付ける企業は少なかったのです。そんな中で加藤研磨製作所は未経験者でも応募を受け付けていましたので、面接を受けてみました。1000分の1ミリ単位で加工できる非常に高度な技術を持っている企業ですし、入社することに決めました。
円筒型部品の外径を削る作業を担当しています。円筒型の部品を削る時には、円の中心を見極めて機械に取り付けないと上手く削れません。自分だけでは分からないことだらけですから、何事も先輩に教えてもらいながら進めています。
少しずつ仕事に慣れてきましたが、知れば知るほど、先輩の持っている技術のすごさが分かるようになりました。例えば、私たちは1000分の何ミリから何ミリまでと指定された寸法の範囲内に仕上げようとします。一方、先輩たちは「ぎりぎりでも良いから範囲内に収める」のではなく、「範囲内のちょうど真ん中の寸法で仕上げる」ことを目指しています。1000分の1ミリどころか、1万分の1ミリの世界で勝負しているわけです。
自分で部品を加工することで、次第に形が整ってくるのが目に見て分かるところが、ほかの仕事と違うところだと思います。図面どおりの形にできると、「やった」と思いますね。
当面の目標としては、自分の担当している円筒研磨の作業を、1人である程度できるようになることです。それができるようになってから、ほかのことにも挑戦していきたいですね。
今はまだ、新しい部品の加工の際にはやり方が分からず、先輩に全部教えてもらっている状況です。近いうちに図面を見るだけで、加工方法を最後まで考えられるようになりたいです。
学生の方の中には、作業着を着て工場勤務をすることを敬遠している方もいらっしゃるのではないでしょうか。でも実際にやってみると、私たちの仕事は非常に高い技術力を求められるのです。誰にでもできる仕事ではなく、すごくやりがいがあります。そんな会社で作業着を着て働くのも、面白いものですよ。
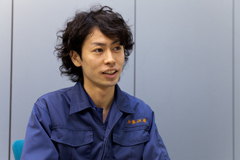
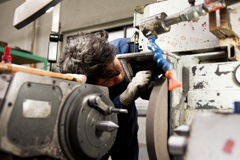